Overhead conductors play a critical role in power transmission, carrying electricity over vast distances to homes, industries, and businesses.
However, these conductors are constantly exposed to environmental, mechanical, and electrical stresses that can lead to failures.
A failed conductor not only disrupts power supply but also poses safety hazards and results in costly repairs.
Understanding the primary causes of overhead conductor failures is essential for preventing unexpected outages and ensuring grid reliability.
Mechanical stress, corrosion, weather-related damage, electrical faults, and improper installation are among the most common reasons for failure.
Each of these factors weakens the conductor over time, increasing the risk of breakage, power loss, and system inefficiency.
To minimize failures, utilities and power companies implement various prevention techniques, including advanced monitoring systems, high-performance conductors, improved installation practices, and real-time maintenance strategies.
Modern innovations like smart sensors, composite-core conductors, and robotic inspections are revolutionizing grid management, reducing failures, and extending conductor lifespan.
Overhead Conductor Main Failure Causes and Prevention Techniques
In this blog post, we will explore the key reasons behind overhead conductor failures and discuss effective strategies to prevent them, ensuring a reliable and efficient power transmission network.
Whether you’re an engineer, utility professional, or industry expert, understanding these critical aspects will help enhance grid performance and reduce operational risks.
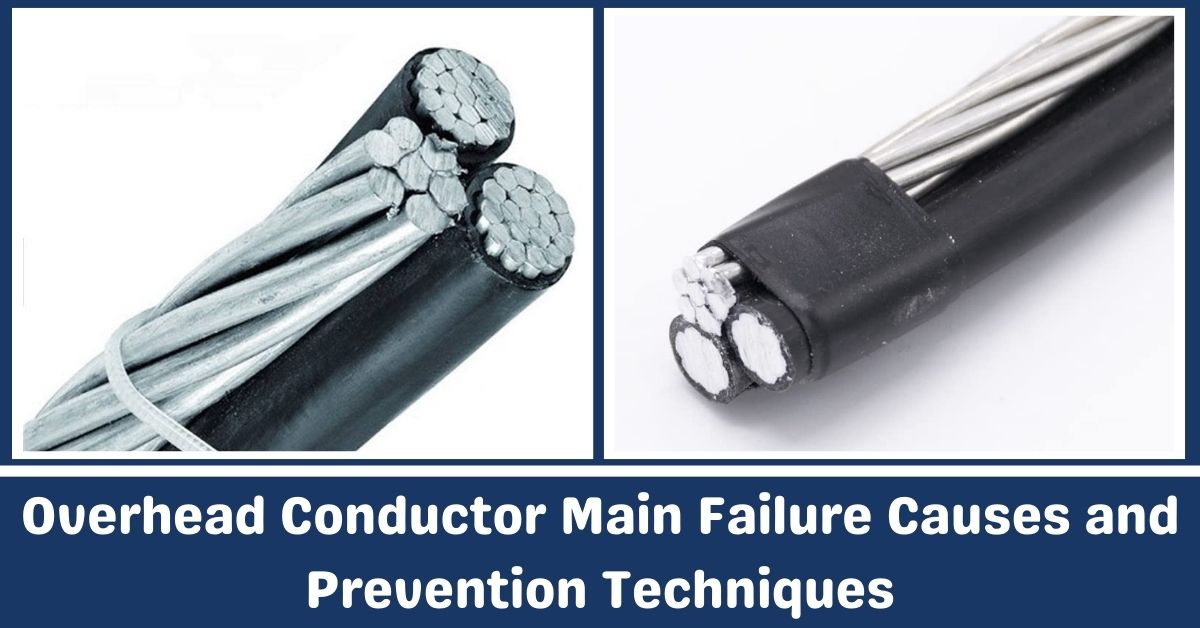
1. Main Causes of Overhead Conductor Failures
Overhead conductors are exposed to various environmental, mechanical, and electrical stresses that can lead to failures over time.
Understanding these failure causes is crucial for preventing power outages, reducing maintenance costs, and ensuring a reliable electricity supply.
Mechanical Stress and Overloading
Overhead conductors are subjected to mechanical forces that can lead to premature failure. These forces include their own weight, tension applied during installation, wind loads, and additional loads from ice accumulation.
Over time, excessive mechanical stress can cause conductors to stretch, leading to increased sag. If the sag exceeds the design limit, it can result in reduced ground clearance, safety hazards, and electrical faults.
Additionally, mechanical overload can cause conductor strands to break, weakening the overall structure and increasing the risk of sudden failure.
To minimize mechanical stress, proper tensioning during installation is essential. Conductors should be selected based on expected loads, and support structures must be designed to handle environmental conditions.
Periodic inspections can help identify early signs of excessive sag or strand breakage, allowing for preventive maintenance before a failure occurs.
Corrosion and Environmental Degradation
Corrosion is a major cause of conductor failure, especially in coastal, industrial, and high-pollution areas. Conductors are exposed to moisture, airborne pollutants, salt, and acidic compounds, which gradually deteriorate the metal.
Galvanic corrosion can also occur when different metals are used in conductors, splices, or hardware, leading to localized degradation.
Over time, corrosion weakens the conductor, reducing its mechanical strength and electrical conductivity.
Preventing overhead conductor corrosion requires the use of corrosion-resistant materials such as aluminum-clad steel or composite conductors. Protective coatings, greases, and weather-resistant sheathing can further enhance durability.
Regular inspections, particularly in high-risk areas, allow for early detection of corrosion. If corrosion is found, affected sections should be treated or replaced before the damage leads to structural failure.
Vibration and Fatigue Damage
Wind-induced vibrations, particularly aeolian vibration, can cause repeated bending stress on conductors. These vibrations occur when steady wind flows across the conductor, creating small amplitude oscillations.
Over time, this cyclic stress leads to metal fatigue, which can cause conductor strands to break, particularly at attachment points such as clamps and suspension hardware.
If undetected, fatigue damage can eventually result in a complete failure of the conductor.
To prevent vibration-induced damage, vibration dampers such as Stockbridge dampers, spiral dampers, or tuned mass dampers are installed along the conductor.
These devices absorb energy from vibrations and reduce strain on the metal strands. Proper sag and tension control during installation also help minimize the risk of fatigue failure.
Regular monitoring of vibration-prone spans allows for timely corrective actions to prevent damage.
Lightning Strikes and Electrical Flashover
Overhead conductors are highly exposed to lightning strikes, which can cause electrical and thermal damage. When a lightning bolt strikes a conductor, it generates an extremely high current that can melt the metal surface, leading to localized weakening.
Repeated lightning exposure can cause cumulative damage, increasing the risk of conductor breakage.
In some cases, lightning strikes result in insulator flashover, where the electrical discharge bypasses the insulation and causes short circuits or power outages.
Lightning protection measures include the installation of ground wires (shield wires) above conductors to intercept strikes and safely dissipate energy to the ground.
Additionally, surge arresters can be used at critical points in the network to limit overvoltage and prevent equipment damage.
Proper grounding of transmission towers is essential to ensure that lightning energy is effectively discharged, reducing the risk of conductor failure.
Extreme Weather Conditions
Severe weather events such as heavy ice storms, strong winds, and wildfires can lead to overhead conductor failures. Ice accumulation adds significant weight to conductors, increasing tension and causing sagging or breakage.
Strong winds can cause conductors to oscillate or gallop, leading to excessive mechanical stress. Wildfires expose conductors to extreme heat, which can weaken the metal and cause failure.
To mitigate the impact of extreme weather, anti-icing conductors and coatings can be used in areas prone to ice storms.
Conductors should be designed to withstand expected wind loads, and proper damping mechanisms should be installed to reduce oscillations.
In wildfire-prone areas, utilities can use fire-resistant conductor coatings and conduct routine vegetation management to reduce fuel sources near transmission lines.
Poor Installation and Maintenance Practices
Improper installation techniques significantly increase the risk of conductor failure. Common issues include tension incorrecting, improper splicing, loose connectors, and misaligned fittings.
Poorly installed joints and connectors create high-resistance points, leading to localized overheating and eventual failure.
Lack of regular maintenance further exacerbates the problem, allowing minor defects to develop into critical failures over time.
Ensuring proper installation requires skilled personnel who follow standardized procedures. Conductors must be tensioned correctly to prevent excessive sag or mechanical stress.
High-quality compression fittings should be used, and splices must be made with precision to maintain electrical integrity.
Routine maintenance, including visual inspections and thermal imaging, helps detect early signs of deterioration, allowing for timely repairs and reducing the risk of unexpected failures.
Electrical Short Circuits and External Interference
Short circuits occur when conductors come into direct contact with each other, support structures, or foreign objects such as trees, birds, or metallic debris.
These events can lead to arc flashes, insulation damage, and conductor melting. Wildlife interference, particularly birds and rodents, can also cause faults by bridging conductors or damaging insulation.
Preventing short circuits involves maintaining proper conductor spacing, using covered conductors in areas with frequent wildlife activity, and installing bird diverters to minimize wildlife-related faults.
Fast-acting circuit breakers and relays help isolate faults quickly, reducing the duration of electrical disturbances and preventing further damage.
2. Advanced Techniques for Preventing Overhead Conductor Failures
Advanced techniques are essential for preventing overhead conductor failures and ensuring long-term grid reliability.
By leveraging modern technology, improved materials, and proactive maintenance strategies, utilities can significantly reduce failure risks and enhance power transmission efficiency.
Real-Time Monitoring with Smart Sensors
Modern power networks use smart sensors to continuously monitor conductor conditions. These sensors track temperature variations, sag levels, vibration patterns, and load fluctuations in real-time.
By analyzing this data, utilities can detect potential failure points and take preventive actions before problems escalate.
Sensor-based monitoring also enables predictive maintenance, reducing the need for costly emergency repairs.
Composite Core Conductors for Enhanced Strength
Traditional conductors use steel-reinforced aluminum, which is prone to sagging and corrosion over time. Composite core conductors, such as those made with carbon fiber or fiberglass cores, offer superior strength and lower sag.
These conductors are lightweight, corrosion-resistant, and capable of handling higher current loads without significant thermal expansion.
By replacing conventional conductors with composite alternatives, utilities can improve transmission reliability and reduce maintenance costs.
Robotic Inspection and Aerial Surveillance
Drones and robotic crawlers are revolutionizing conductor inspections. Drones equipped with high-resolution cameras and infrared sensors can quickly scan transmission lines for damage, corrosion, or overheating.
Robotic crawlers can move along conductors, performing close-up inspections without requiring power shutdowns.
These technologies improve inspection efficiency and enable early fault detection, preventing failures before they occur.
High-Temperature, Low-Sag (HTLS) Conductors
HTLS conductors are designed to withstand higher operating temperatures while maintaining minimal sag. They allow for increased power transmission capacity without requiring major infrastructure upgrades.
These conductors use advanced materials such as aluminum-zirconium alloys and composite reinforcements to handle extreme conditions, making them ideal for high-load transmission lines.
Undergrounding in High-Risk Areas
In regions with extreme weather conditions, utilities are increasingly considering underground power lines as a long-term solution.
While underground cables are more expensive to install, they offer complete protection from wind, ice, lightning, and wildfires.
Undergrounding is particularly beneficial for urban areas, coastal regions, and wildfire-prone zones where reliability is a priority.
Conclusion
Preventing overhead conductor failures is crucial for maintaining a reliable power grid, minimizing outages, and reducing maintenance costs.
Failures can result from mechanical stress, corrosion, weather conditions, electrical faults, and poor installation practices. Identifying these risks early allows for targeted preventive measures, improving system longevity and efficiency.
Advanced prevention techniques, such as real-time monitoring with smart sensors, composite core conductors, robotic inspections, and high-temperature low-sag conductors, provide utilities with modern solutions to enhance reliability.
Additionally, proactive maintenance strategies, including routine inspections, vibration control, and wildlife protection measures, further reduce the likelihood of unexpected failures.
Investing in cutting-edge technology and proper maintenance not only prevents costly repairs but also ensures safety, efficiency, and long-term sustainability of power transmission systems.
As power demand continues to grow, utilities must adopt these advanced techniques to build a resilient and failure-resistant electrical infrastructure.
By implementing these solutions, the risk of conductor failures can be significantly minimized, ensuring uninterrupted power supply and long-term grid stability.